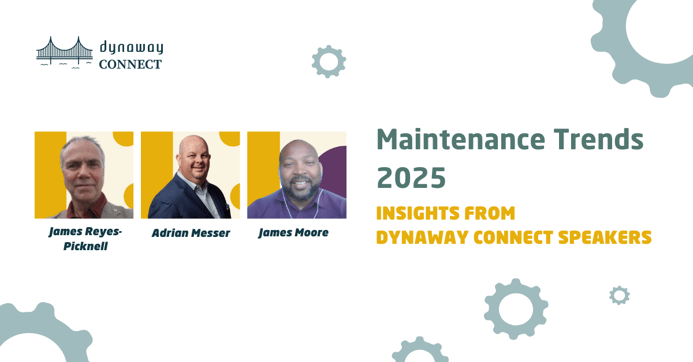
With the new year 2025 just starting, we are reviewing past maintenance trends and looking ahead to what's on the horizon.
Maintenance has always been an important element contributing to business success, but in recent years the field has faced unprecedented challenges (and opportunities!) connected to the rapid integration of new technologies such as artificial intelligence (AI) and internet of things (IoT).
Now, in 2025, the conversation has moved from observing and experiencing these changes to proactively preparing for what’s coming. What lessons can we take from the past few years? What innovations will have the greatest impact moving forward? How can we adapt to these innovations already? These are the questions driving the dialogue in maintenance nowadays.
To take a closer look into these topics, we had the pleasure of talking with some of the leading voices in the maintenance field – our Dynaway CONNECT 2025 speakers. We contacted three upcoming speakers and asked them three key questions concerning the past, the near future, as well as a piece of advice they would offer from one maintenance professional to another.
The answers came from James Reyes-Picknell, Adrian Messer, and James Moore.
Question 1:
What do you believe has changed the most in the maintenance field in recent years?
James Reyes-Picknell:
"There have been a number of changes including the loss of experienced older workers, the increased difficulty in finding skilled craftspersons, and a hyper-focus on costs that is increasing risks and lowering overall performance. The baby boomers are largely gone now. That has brought about a loss of corporate memory since companies did a terrible job of knowledge transfer."
One of the major changes in the maintenance field outlined by James is the generational transition. Unfortunately, this change led to an issue that many organizations face today: the departure of older and more experienced workers has created a knowledge gap difficult to fill. This usually happens due to a lack of proper knowledge transfer mechanisms. To address this challenge, organizations must incorporate structured, documented workflows to ensure the expertise is preserved and doesn’t get lost once an employee retires.
"Leadership wasn't immune from that trend either. There are new and younger people in all levels of the corporate ladder and many seem uncomfortable with challenging established rules. They haven't quite learned that you can't fix problems with the same thinking that created them."
Another result of generational transition is the younger generation of leaders bringing fresh perspectives. However, according to James, those leaders are often not confident enough to challenge the status quo, and therefore“The result is overly conservative decision making that isn't well informed or subjected to critical thought.”
Moreover, the reliance on technology is excessive:
"They actually believe that technology will provide answers, but after some 60 years since the first CMMS emerged, we should know better. There is a heavy emphasis on technology today and it is in all areas of our lives. For the most part, it works well and makes many of our daily tasks easier. For individuals, it's great. But in business, the tasks are not so simple. The business environment is complex with many individuals, many different tasks, and many different and often competing objectives. Those skilled programmers and developers who can enable you to order your coffee and skip the line for pick up don't have much insight into business processes and the need for their integration. They have little advice and what they get comes from those who have gone through business school, not the school of hard knocks. Business systems simply don't work as well, and we see that in maintenance. Despite millions being spent on software, and sometimes even training in how to use it, we still can't seem to get parts to the trades to carry out a planned job on schedule."
While technology systems work well when simplifying individual tasks, their integration into complex business processes is much more challenging, and there is still plenty of room for improvement. The issue isn’t with the technology itself but rather with how organizations approach the implementation. The business processes should be clearly defined and aligned with the capabilities of the technology being adopted.
"All that is happening in an environment where the focus is increasingly on ‘shareholder value’ - meaning profit and share price. Workers are expendible and customers are an abstract concept left to deal with voice jail and automated bots chatting with them. Perhaps it is cheaper than the alternative but is it what customers really want?"
Investing in technology is another latest change. Companies are cutting costs and replacing support with AI chatbots. But are they really as efficient as humans? They can handle basic queries; however, they fall short when it comes to delivering the empathetic and personalized service that our customers expect.
"As we cut costs, we give up the ‘discretionary’ spending on training and external help that could help us make up for some of the problems we have because we've lost our corporate memory and ability to think things through all the way. Our organizations are too lean to afford the luxury of moving up the corporate equivalent of Maslow's hierarchy of needs. Cost only translates into value in one very narrow perspective. Accountant / bookkeeper thinking has to get out of the way and allow business decision making, or risks will rise along with incidents and accidents of all sorts (we are already seeing a lot of this) and performance will continue to disappoint."
According to James, an overly narrow focus on financial metrics comes with a risk. The takeaway here is rather clear: giving up the ‘discretionary’ spending leads to broader implications. Through the analogy of Maslow’s hierarchy of needs, James argues that it is hard to achieve higher levels of performance in organizations that operate in a constant state of cost-cutting. For organizations to thrive, they must invest strategically in people, tools, and processes to be able to reach the top levels of the pyramid – self-esteem and self-actualization.
Adrian Messer:
"I think that maintenance and reliability technology, hardware, and software have seen the most changes in recent years. Technology & software may have changed, but the fundamentals remain the same, and training & developing your maintenance & reliability workforce have never been more important than now."
James Moore:
"Reporting Metrics and Diagnostics."
Question 2:
What trends do you foresee having the most significant impact on maintenance in the near future?
James Reyes-Picknell:
"A positive trend is towards the use of artificial intelligence. Specifically, I see value in how it can increase productivity, once we get over the survival fears that it will take our jobs. I don't believe it can take away jobs that require the use of our bodies - so trades are safe. I don't believe it will ever replace leadership - we need leaders who rock the boat. I believe it can enhance productivity in tasks that are tedious and detailed such as developing reports and planning. It can follow rules and help us get more done, more quickly.
I've even worked with colleagues to develop an AI enabled job planning tool for maintenance. It works very well and gets better (smarter) every day, but it won't replace the planners who seem so fearful of it. Planners are often constrained by the limits of their own trade's background. The tool doesn't have a trade so that's not a constraint. Planners work at human speeds. The tool works at the speed of electrons. Planners research within the available information in their office or on their corporate systems. The tool researches that plus every piece of related information that has ever been put online, anywhere. Instead of producing 1 to 5 plans a week, it produces upwards of 40 or more, allowing for the time needed to review its output. It's not perfect, so whatever it produces needs to be reviewed and edited, but that takes far less time than starting from scratch. It won't replace planners, but it can make them far more productive.
Another trend that I'm spotting, and it's based on gut feel resulting from reading the news. Incidents and accidents seem to be trending upwards. There are more equipment breakdowns that are making the news. This trend is very negative, and it is evidence of our failure to learn from past mistakes. These events will teach lessons and many of those lessons will be repeats of the past. Our newer, younger, less experienced workforce will continue to gain experience through these lessons, and some of them will be tough lessons. It's a trend that is well worth reversing, but we'll need to get our minds out of the ruts created by the accountants to achieve it."
Adrian Messer:
"Continued push for sensor technology, data integration, and the increased need for electricians, controls technicians, and automation engineers."
James Moore:
"Preventative Maintenance. Becoming a more proactive than reactive maintenance program and increasing the utilization of technology for maintenance workers to assist in cutting down diagnostic time to focus on repair time."
Question 3:
What is one piece of advice that you consider especially valuable to professionals in the maintenance and reliability sector?
James Reyes-Picknell:
"See technology as a tool and stop seeing it as 'the way' or as a 'solution'. Computers do what they are programmed to do. Even AI does that. Their programmers are truly brilliant with technology, but most have little knowledge of fields like finance, operations, maintenance, reliability, spares management, procurement etc. Take back our processes and start looking beyond just M&R into its supporting functions of spares, procurement and collaboration with operations for ways to improve what we do."
Adrian Messer:
"You can’t maintain your way to reliability. A decision to implement reliability is a business decision and is best implemented when everyone within the organization understands their part in operating more reliably."
James Moore:
"Be involved in the makeup and maturation of your maintenance program. Don’t be on auto pilot and get stuck in the 'This is how things have always been' mindset. Maintenance is always growing, changing and expanding and you must grow and change with it. Becoming less mechanical and more computerized. Adjust your maintenance program and worker mindset."
New Trends in Maintenance
Mike Mason is the Director of Maintenance Reliability Services at ERP Automated, a professional services provider that specializes in maintenance reliability and Dynamics 365 Supply Chain.
Mike was our speaker at Dynaway CONNECT 2024, and he also shared with us his insights on new trends in maintenance:
You can find the full interview with Mike on our Spotify channel:
About our CONNECT 2025 Speakers
If you are not yet familiar with James Reyes-Picknell, Adrian Messer, and James Moore, you can learn more about them in this section.
James is a co-founder and President of Conscious Asset and the author of some incredible books on maintenance and reliability, like "Uptime – Strategies for Excellence in Maintenance Management" and "Reliability Centered Maintenance – Re-engineered". James has a background in mechanical engineering from the University of Toronto and more than 43 years of experience in maintenance, reliability, and asset management. Over his career, he’s worked in all kinds of industries, from hands-on technical roles to leadership positions. He eventually moved into consulting, working with IBM Business Consulting Services (formerly PwC Consulting, PricewaterhouseCoopers and Coopers & Lybrand), before founding his own firm, Conscious Asset, 20 years ago.
Adrian Messer is a US Operations Manager at SDT Ultrasound Solutions. He has been involved in the Maintenance and Reliability field since 2003, working with manufacturing and facilities across various industries to enhance their asset reliability through improved asset condition monitoring programs. His expertise lies particularly in airborne and structure-borne ultrasound technology. In his role as US Operations Manager for SDT Ultrasound Solutions, Adrian is dedicated to educating, implementing, and supporting ultrasound technology in energy conservation and asset condition monitoring programs. Adrian holds a Bachelor of Science in Management from Clemson University. He is also a Certified Maintenance and Reliability Professional (CMRP) through the Society for Maintenance and Reliability Professionals (SMRP) and a Certified Reliability Leader (CRL) through the Association of Asset Management Professionals.
James is an EAM Product Manager and former Vehicle Maintenance Manager in IndyGo, with 17 years of experience in the transportation industry. He has expert knowledge in vehicle maintenance, including installing, maintaining, and repairing systems like mechanics, electrical work, HVAC, and vehicle structures. James also has a strong background in safety practices, including knowledge of personal protective equipment (PPE), chemical hazard protocols, lockout/tag-out procedures, and maintaining overall shop safety and cleanliness.
With hands-on experience in Microsoft Dynamics 365 F&O (now Finance & Supply Chain Management) and certification in Dynaway Enterprise Asset Management, James has successfully led multiple vehicle maintenance projects.
Conclusion
To sum up, the emerging maintenance trends include:
- - Increased adoption of AI and IoT for predictive and condition-based maintenance
- - Sensor technology and data integration to improve asset performance and monitoring
- - Proactive maintenance programs that prioritize efficiency and minimize downtime
- - A growing focus on workforce development. Ensuring teams are prepared for technology-intensive environments
However, despite these advancements, our experts agree that the future of asset management and reliability lies in the balance between embracing innovation and traditional, proven practices - success doesn’t come from relying solely on modern, new technologies like AI or IoT. Rather, it requires a well-knit combination of these practices with the conventional approaches. In other words: advancements can’t replace the value of human expertise and foundational processes. Instead, they can be integrated with established methods.
As emphasized by James Reyes-Picknell, while technology is power, it can't be the only solution to our complex problems. Similarly, Adrian Messer mentioned the potential of sensor technology and data integration while reminding us that the fundamentals of maintenance, such as employee training, remain critical.
James Moore advocated for proactive maintenance programs that use technology to reduce downtime and improve repair efficiency. His stance aligns with industry reports highlighting that companies adopting proactive approaches, such as predictive maintenance, can reduce unplanned machine downtime by as much as 50%.
The collective insights from these experts suggest that the future of asset management and reliability will be shaped by professionals with mindsets open to innovation but also remaining dedicated to building strong teams, ensuring knowledge transfer, encouraging collaboration, and, last but not least, learning from past mistakes. By integrating advancements to enhance - not replace - human expertise and foundational processes, professionals can ensure that innovation is guided by experience and wisdom.
The future of asset management and reliability is here, calling for harmony between innovation and established workflows. The question remains: How will you contribute to shaping this future?