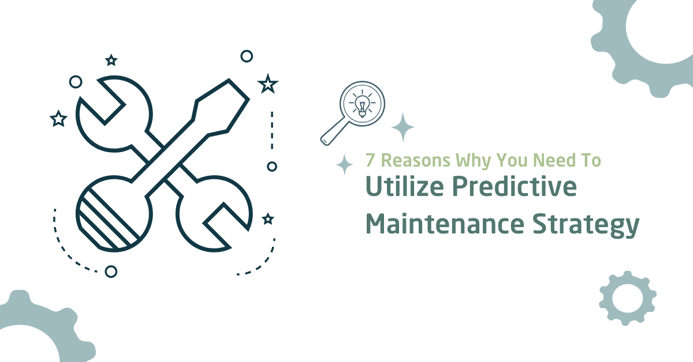
The International Society of Automation (ISA) estimates that manufacturers lose $647 billion globally every year to downtime. That is a financial leak that businesses can not afford in today's competitive landscape. In response to this financial wake-up call, a revolutionary concept has been progressively becoming more popular: Predictive Maintenance.
KEY TAKEAWAYS
- Predictive maintenance (PdM) is a strategy where assets and equipment are constantly monitored in real-time to prevent potential issues.
- Embracing predictive maintenance is a wise investment that can help businesses stay competitive in today's technology-driven world and pave the way for a more efficient and sustainable future.
- Predictive maintenance benefits include enhanced operational efficiency, cost savings, improved safety, sustainable production, better inventory management, improved product quality, and increased customer satisfaction.
- Transitioning from reactive maintenance to predictive maintenance requires a change in mindset, processes, and technology adoption, and expert support can be valuable in making this transition successful.
What is Predictive Maintenance?
Predictive maintenance (PdM) is a condition-based maintenance strategy relying on monitoring assets and equipment in real-time. It utilizes data and analytics to predict when equipment or machinery is likely to fail, allowing for proactive maintenance before any breakdown occurs.
Predictive maintenance not only saves time and money but also prevents costly downtime and potential safety hazards through data-driven decision-making.
How is Predictive Maintenance performed?
Predictive maintenance is performed using advanced technologies, data analysis techniques, and monitoring processes. These procedures allow maintenance professionals to forecast potential equipment failures and schedule maintenance activities accordingly, ensuring optimal equipment performance and reducing unexpected downtime.
Through the use of sensors and monitoring devices, equipment performance parameters are constantly monitored, collecting valuable data on the operating conditions and performance trends. This data is then analyzed using algorithms and machine learning techniques, allowing maintenance professionals to determine patterns and anomalies that could indicate potential issues. These insights enable maintenance teams to take timely action, addressing minor problems before they escalate into major failures, leading to significant cost savings and improved equipment reliability.
Predictive Maintenance Software
Predictive maintenance software solutions utilize advanced analytics and IoT technologies to analyze data and make predictions.
As for the type of software used for predictive maintenance, there are various options available in the market, including IBM Maximo and SAP Predictive Asset Insights.In case your organization is using Microsoft Dynamics ERP, Dynaway EAM would be a perfect match.
Read more: 10 Common Worries When Choosing EAM Software (And How To Manage Them)
The Benefits of Predictive Maintenance
1. Enhanced Operational Efficiency
One of the key benefits of utilizing a predictive maintenance strategy is the significant improvement in terms of operational efficiency.
Predictive maintenance allows businesses to identify and address potential equipment failures before they happen, reducing the risk of unexpected breakdowns and production downtime. As a result, not only is equipment lifespan extended, but production targets are consistently met without interruptions.
Through leveraging data, organizations can make informed decisions about maintenance schedules and resource allocation, ensuring that maintenance activities are performed at the most convenient times.
2. Cost Savings
Predictive maintenance can contribute to cost savings in your organization.
In fact, due to the research article "Methodology for data-driven predictive maintenance models design, development and implementation on manufacturing guided by domain knowledge",the implementation of predictive maintenance systems can save up to 60% of maintenance costs.
Enterprises can avoid costly repairs and replacements by identifying and addressing maintenance needs before they become significant issues.
3. Improved Safety
The construction sector in the United States is recognized as one of the most hazardous industries, with 951 occupational deaths in 2021, according to the U.S. Bureau of Labor Statistics. The four primary hazards emphasized by the Occupational Safety and Health Administration (OSHA) in construction— falls, struck-by incidents, electrocutions, and caught-in/between accidents— continue to pose significant risks to the safety and lives of workers in this field.
Predictive maintenance helps identify potential safety hazards before they cause accidents or injuries. By continuously monitoring equipment performance and analyzing data, organizations can detect any abnormalities or deviations that may indicate a safety risk.
For example, if a sensor detects a sudden increase in temperature or vibration levels in a machine, it could indicate a potential malfunction or failure that could pose a safety risk. By receiving real-time alerts and notifications, maintenance professionals are able to quickly investigate the issue and take appropriate measures to prevent any accidents or injuries.
In addition to identifying safety hazards, predictive maintenance also enables organizations to prioritize maintenance tasks based on their level of risk. By analyzing data and identifying critical equipment or components that are more prone to failure, maintenance teams can allocate their resources effectively and focus on addressing high-risk areas first.
It is of the highest importance to address maintenance needs promptly to create a safer working environment for the employees. That contributes to the well-being of workers and aligns with the social aspects of sustainability.
4. Contribution to Sustainable Production
Beyond purely economic aspects, a predictive maintenance strategy aligns with a company's efforts to address the aspects of sustainable and responsible production.
In today's world, sustainable manufacturing has become a core requirement - manufacturing processes are expected to minimize their influence on the environment throughout their entire life cycle. Sustainability in the manufacturing sector involves a holistic approach, including taking care of the environment, making sound economic decisions, and considering the well-being of society.
As cost savings and the well-being of employees in connection to their safety have already been discussed in the points above, let us focus on the environmental factor of sustainable production.
- Minimizing Parts and Material Waste
Equipment failures often result in scrapped or defective products, leading to material waste. Predictive maintenance helps prevent such failures, reducing waste.
Besides, emergency repairs can involve the replacement of entire components or parts, even if they are not entirely worn out. Predictive maintenance ensures that components are replaced only when necessary, reducing parts waste.
For example, imagine that through predictive maintenance, you are able to detect early signs of wear in a conveyor belt. Instead of replacing the ENTIRE belt prematurely, only the worn sections are replaced, minimizing material waste.
- Decreasing Hazardous Waste
Picture the scenario: you are standing in a bustling chemical processing plant, surrounded by the constant hum of machinery. Suddenly, an alarm goes off, indicating a potential pump failure. The stakes are high, with the risk of a hazardous chemical spill looming.
Some equipment failures may lead to hazardous material spills or releases that could harm the environment and incur substantial cleanup costs. Predictive maintenance helps prevent such incidents - its ability to anticipate and address equipment issues before they escalate into failures makes it a practical tool for a safer, greener world.
- Enhancing Energy Efficiency
Predictive maintenance facilitates more intelligent scheduling of equipment operation. This may involve running high-energy-consuming equipment during off-peak hours or shutting down machinery when not in use, further enhancing energy efficiency.
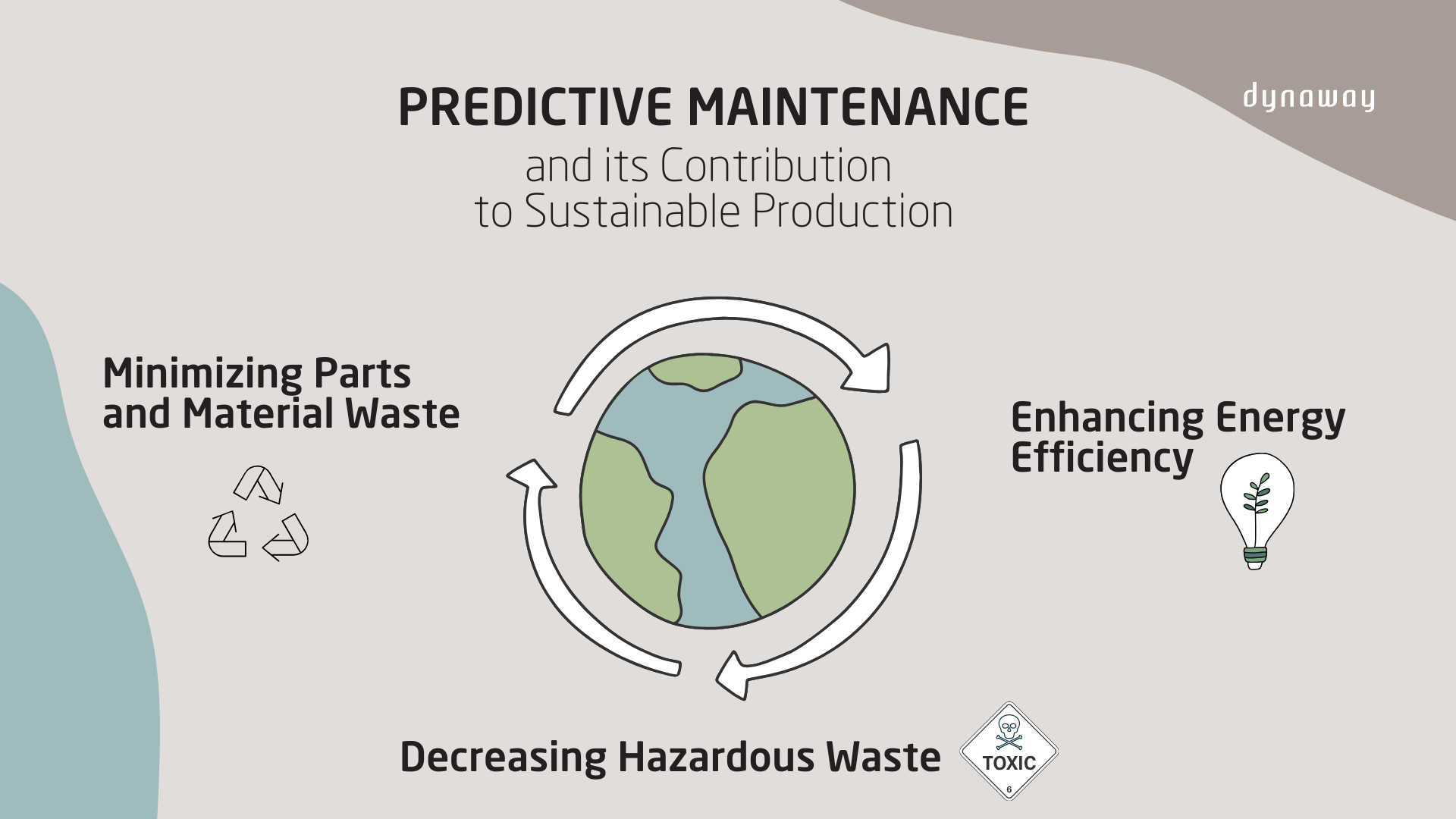
5. Better Inventory Management
Predictive maintenance helps organizations plan and manage their spare parts inventory more effectively. As predictive maintenance systems can forecast when equipment is likely to fail based on data analysis, the organizations anticipate which spare parts will be needed in the near future.
For example, if a system predicts that a critical machine's bearings are likely to fail in the next month, the organization can order the necessary bearings in advance to have them ready when needed. Instead of stocking a wide range of spare parts for all machines, they focus on procuring only the specific components necessary for the asset with the predicted issue.
In this way, businesses can ensure that they have the must-have supplies on hand while reducing inventory costs and minimizing downtime.
6. Improved Product Quality
When a manufacturing plant utilizes predictive maintenance and notices a slight irregularity in a critical machine's performance, such as increased vibration or temperature fluctuations, maintenance employees can take immediate action. This might involve fine-tuning the machine, replacing a worn component, or adjusting operating parameters to bring it back into optimal condition.
Thanks to addressing the abnormalities immediately, the organization avoids potential deviations in product quality and maintains consistency in its production processes.
In short, predictive maintenance safeguards product quality.
7. Increased Customer Satisfaction
Last but not least.
In today's highly competitive market, customer satisfaction is more important than ever, and predictive maintenance plays a role in enhancing it.
When equipment malfunctions or breaks down unexpectedly, it can ripple through the production process, causing delays that extend to service delivery and disrupt the entire supply chain, resulting in customer frustration and dissatisfaction.
With predictive maintenance in place, businesses can proactively identify and have potential issues covered before they impact the customer experience. This helps in ensuring a more responsive supply chain and better customer service.
With the ability to anticipate equipment failures and schedule maintenance activities accordingly, businesses can minimize the impact on customer operations and provide timely solutions that align with customer expectations.
From Reactive to Predictive Maintenance
Making the shift from reactive maintenance to more efficient approaches, such as predictive maintenance, can be a challenging endeavor for numerous companies. It requires a change in mindset, processes, and technology adoption. Engaging a team of experts can provide invaluable support in navigating this transition successfully.
Dynaway has proven experience in implementing Dynaway EAM for Microsoft Dynamics - we assist our clients in accomplishing the transition from reactive to preventive and predictive maintenance practices.
"Dynaway stands out for our extensive expertise and focus on Enterprise Asset Management (EAM) for Microsoft Dynamics. With years of successful implementations, Dynaway has demonstrated a deep understanding of Dynamics ERP, making us the go-to partner for businesses seeking to transition from reactive to predictive maintenance.
Our proven track record in EAM, coupled with a specialized approach tailored to companies with a MS Dynamics strategy, ensures effective, cost-saving maintenance strategies and operational efficiencies.
This expertise, backed by years of experience and successful projects, positions Dynaway as a leader in asset management solutions for Dynamics ERP environments.
-Ulrich Kærgaard, Managing Director at Dynaway.
Conclusion
Implementing a predictive maintenance strategy provides organizations with many strategic advantages. This approach is not just a passing trend; it stands as a proven method to prevent costly breakdowns and optimize the performance of valuable assets.
Nevertheless,it is important to acknowledge that, in some cases, limited data availability can pose a challenge to the implementation of a predictive maintenance strategy. Despite that, businesses should consider predictive maintenance as a smart investment to prevent costly breakdowns and optimize the performance of valuable assets.
To learn more about predictive maintenance and overcome data limitations, organizations can explore various predictive maintenance software solutions available in the market.