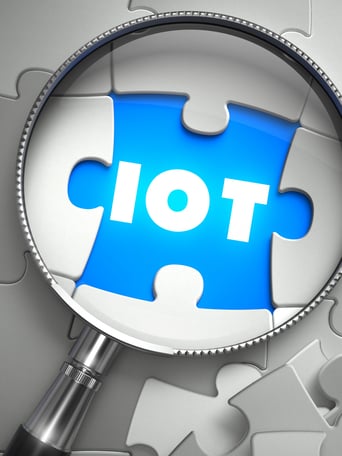
1. Condition Monitoring: Let your assets talk to you
Just like us, assets can speak.
Their talk and their words consist of parameters and signals such as vibration, temperature, viscosity, decibels, wear particles, corrosion, and a whole lot more.
And when things get bad, the assets shout at us. The severity of their words goes up and up.
They tell us they are in poor health or bad condition.
Are you really listening? If you are, you are already performing some form of condition monitoring.
2. IoT sensors in Maintenance
Where do you start with IoT in maintenance?
Whether you are a small manufacturer of a popular craft beer or a multi-national petrochemical plant, IoT sensors and predictive maintenance (PdM) are affordable and accessible to all.
Read more about IoT Predictive Maintenance Technologies and Sensors.
3. 5 Reasons IoT Projects Fail and How to Avoid It
Many Industrial IoT projects fail.
Many IIoT value chains have ended up with broken, rusting links.
That’s been a disappointing fact of life so far for many organizations on the IIoT and industry 4.0 journey to digital transformation and operational optimization.
Let’s take a look at some of the key reasons for failure and how to increase your chances of IIoT project success.
4. Vibration & IIoT Sensors
Vibration analysis is a key technology in the ever-changing world of IIoT and predictive maintenance.
It may be the key technology for assessing the health of rotating assets in industry and giving your organization an early warning of deterioration and impending asset failure.
It drives high asset availability through the life cycle.
But what’s it all about?
Read the article and find out!
5. The Top 5 Benefits of Condition-Based Maintenance in the Age of The IIoT
Digital, big data is constantly streaming back to the cloud and then through IoT value chains for higher and higher predictive maintenance performance. This is transforming the maintenance programs of those enlightened companies that strive for excellence, business intelligence, and real-time data analysis in their physical asset management strategies.
Learn what are the top 5 benefits of CBM.
6. Reliability & Availability: How to Get There with FMEAs and P-F Curves
Failure Modes & Effects Analysis: getting to the bottom (or top) of things
For organizations that suffer from unexpected failures and unplanned downtime, Failure Modes and Effects Analysis (FMEA) can help achieve high asset reliability and availability.
You get reliability and availability right, and you are a long way down the road to profitability.
But here’s a surprise.
Many organizations and manufacturers never make this journey and happily continue (if useable product is getting to the customer on time) in a downward spiral.