In 2019, facing outdated processes and inefficiencies, IndyGo embarked on a transformative journey by partnering with Dynaway. The new EAM system, seamlessly integrated with Dynamics AX 2012, brought a host of innovations: mobile access to work orders, timely servicing through counter-based maintenance, and powerful reporting features. This successful implementation not only enhanced operational efficiency but also set the stage for ongoing improvements in fleet management.
Dive into the full story to see how IndyGo is driving into the future of fleet management.
In today's world, public transportation plays a crucial role in connecting people and places. As our cities continue to grow and evolve, the need for reliable transit systems becomes increasingly evident.
Public transportation is not just a way to get from point A to point B. It enables access to work, education, and leisure for everyone, while also reducing traffic congestion, cutting emissions, and creating more sustainable communities. Whether in bustling metropolises or serene suburban areas, public transit infuses energy and vitality into the heart of modern civilization.
But behind the scenes, ensuring that buses, trains, and trams run smoothly involves a complex web of planning, maintenance, and innovation. In this article, we will explore the world of transportation with IndyGo buses, our valued customer.
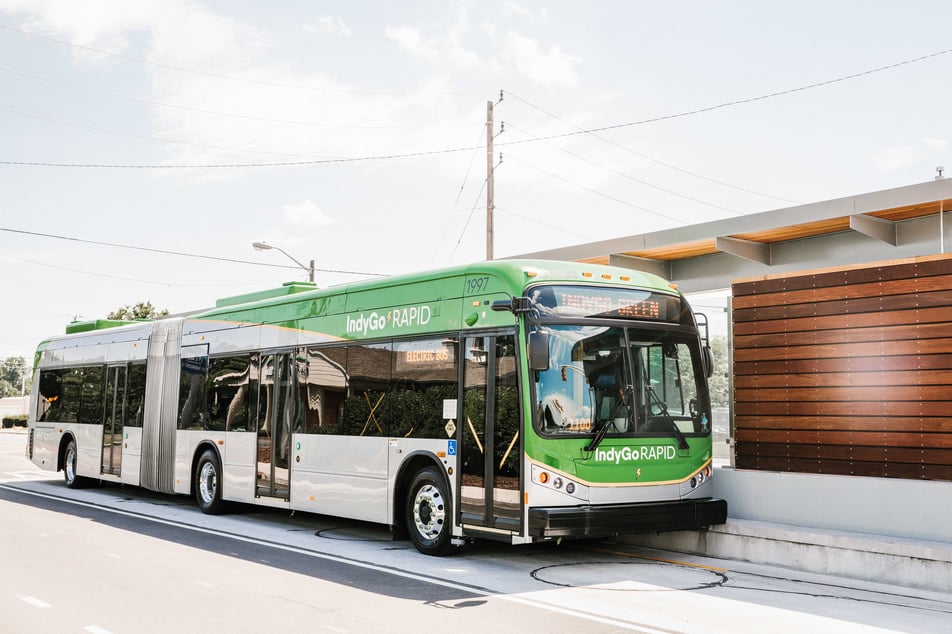
Source: IndyGo Bus on flickr
Introduction
The story of IndyGo—Indianapolis Public Transportation Corporation lies in the heart of Indianapolis, where the city's pulse beats strongly.
IndyGo, a cornerstone of Indianapolis Public Transportation, has served the city for nearly 80 years. From its beginnings with horse-drawn carriages to today's modern bus fleet, IndyGo has continuously evolved to meet the community's needs.
IndyGo's mission is to empower their community by fostering connections through accessible, fair, and inclusive mobility solutions. Ensuring the provision of safe and dependable transportation is crucial to delivering a service that customers can rely on and trust while also safely transporting their loved ones.
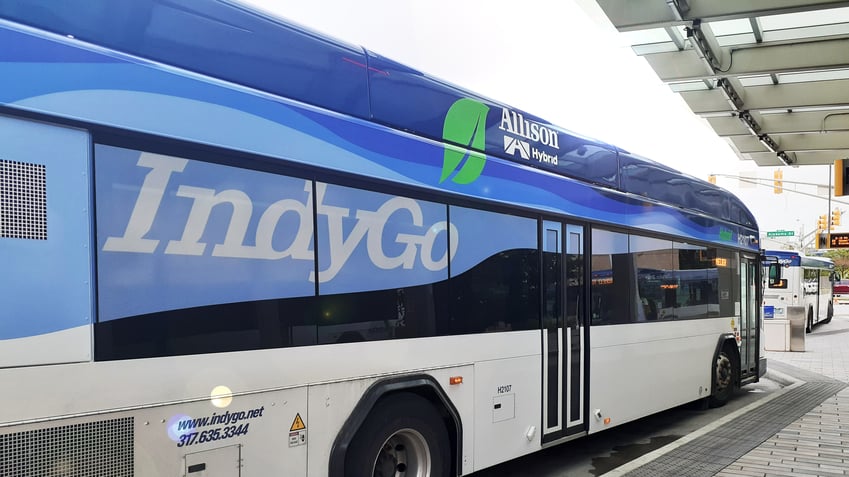
Source: IndyGo Bus on flickr
IndyGo has been a valued Dynaway customer since 2019. We had the pleasure of speaking with James Moore, who previously served as Vehicle Maintenance Manager and now holds the role of EAM Product Manager at IndyGo.
James transitioned into the project management team as the EAM Product Manager a few months ago. In this role, his primary responsibility is ensuring the smooth operation and regular updates of the EAM system. He addresses any issues or needs from various company departments that utilize the system. Additionally, James is responsible for integrating other platforms with the EAM system, particularly D365 F&O, to streamline inventory, warehouse, and procurement processes.
During our conversation, James shared valuable insights into IndyGo's maintenance evolution, emphasizing the progress made in enhancing operational efficiency and system integration: "Dynaway has helped us become more efficient in our work process (...). Dynaway Mobile parts requisition has revolutionized how our mechanics wreck out parts and how our inventory warehouse maintains and requisitions those parts."
You can watch the interview here:
This article highlights the collaborative partnership between IndyGo and Dynaway, emphasizing their dedication to maintenance excellence.
The Challenge
In the transportation industry, outdated or inadequate maintenance software can lead to significant operational challenges and difficulties in adhering to the stringent maintenance processes required by the Federal Transit Administration (FTA) rules and guidelines. IndyGo faced this hurdle head-on.
Initially, IndyGo operated using a basic system designed for the mining industry, resulting in a highly manual and inefficient process.
"We were utilizing maintenance software called Ellipse, which was actually a defunct mining maintenance software that we were using. And I came to find out later that the software had been used in a dummy state since about 2015. Really, the capability of that software was very minor. Essentially, it was just kind of writing work on a piece of paper and saying here, go do this."—explained James Moore, EAM Product Manager at IndyGo.
James shared information about IndyGo's prior processes with us. Handwritten work orders provided minimal information, simply instructing mechanics to "repair" without specifying the time, parts, or labor involved. This manual method hindered the accurate tracking of maintenance activities, causing inefficiencies and potential operational disruptions.
Struggling to maintain efficiency and reliability in fleet operations, IndyGo recognized the urgent need for a transformative solution to ensure the seamless functioning of the city's transportation network.
Choosing a New EAM Solution
When selecting a new Enterprise Asset Management (EAM) solution, several key criteria guided IndyGo's decision-making process:
- Integration with other systems
- Capabilities
- Record-keeping
- Condition-Based Maintenance (CBM)
- Deployment process
Let's zoom into each of them.
1. Integration with other systems
After Ellipse, IndyGo transitioned to Dynamics AX 2012 to manage its finance and inventory operations, which meant its new maintenance software had to seamlessly integrate with this system. This compatibility was crucial to ensuring cohesive and efficient operations across their financial and maintenance departments.
2. Capabilities
Another significant criterion was the software’s capability to manage comprehensive maintenance tasks. It was essential that the new EAM solution could handle work orders, generate preventive maintenance services, and support detailed maintenance checklists. The goal was to streamline these processes to enhance efficiency and ensure all necessary maintenance activities were thoroughly documented and executed.
3. Record-keeping
Additionally, robust record-keeping functionality was imperative. IndyGo's previous system lacked consistent record-keeping, which often led to operational inefficiencies. The new system needed to provide a reliable means of maintaining detailed maintenance records, thus improving our ability to track and manage our assets effectively.
4. Condition-Based Maintenance
Moreover, the ability to utilize condition-based maintenance was an important feature. IndyGo's external Fleetwatch system monitors various metrics such as fluid consumption and mileage, and they needed an EAM solution that could integrate this data to predict and schedule maintenance activities accurately. This integration helps IndyGo perform maintenance every 6,000 miles, ensuring timely servicing and reducing the risk of breakdowns.
5. Deployment Process
Finally, the deployment process and the system’s flexibility were also taken into consideration. IndyGo required a solution that could be tailored to their unique needs and one that their team could learn and adapt to within a reasonable timeframe.
Implementation Process
James Moore shared with us information about the implementation process:
"As far as the actual implementation of Dynaway, I wasn't the one that particularly chose the product. But when it was brought in, I was one of the ones, particularly on the maintenance side, that really took ownership of it and made sure that we at least tried to utilize the system to the best of our ability and made sure that the system did what we needed it to do."
The implementation took several months, during which IndyGo focused on training and customizing the system to meet our specific needs, ensuring a smooth transition and effective utilization of the new EAM solution.
"Dynaway was a great partner, getting us whatever we needed to meet our needs, finding out what we needed to do to get through the process." – shares James.
Managing the Change
Navigating change during the implementation of a new system is an unavoidable part of progress.
"Change is always difficult for most people," - acknowledged James Moore. -"But as long as you have constant communication and training, you have to get people used to the system. Otherwise, they're going to be scared to do something new. They would think they are going to mess something up."
IndyGo went above and beyond by providing hands-on training sessions to empower employees to familiarize themselves with the new system at their own pace. They also highlighted the tangible benefits of the new system to experienced employees who have been used to established routines, demonstrating how it would streamline processes and simplify tasks to foster a positive attitude towards change.
James emphasized the importance of leading by example and guiding employees through the transition to ensure their comfort with the new system: "You can't just roll out a new product and expect people to adopt it. You have to guide them, show them you're comfortable with the system. If you're not comfortable, they won't be either."
Impact on the Business
IndyGo has experienced significant changes through using Dynaway EAM. We asked James, IndyGo's representative, about the top advantages of Dynaway. Here's the list:
1. Mobile Platform
A major advantage is a flexibility gained, thanks to the mobile platform, which allows workers to easily access their work orders.
"One of the top advantages is Dynaway's flexibility, particularly with the mobile platform that's been provided. Our workers have much easier access to their work orders without having that physical work order that they may lose track of and don't know exactly what they're supposed to be doing. It's accessible; they can have it on their phone, on a tablet, or maybe a workstation that's set up in the shop." - as explained by James Moore.
2. Supporting Condition-Based Maintenance
Besides, as mentioned already earlier, Dynaway supports IndyGo when it comes to condition-based maintenance. That is imperative for a business in the transportation industry as it guarantees regular vehicle maintenance, reduces downtime, prevents unexpected breakdowns, and maintains safety, thus improving overall reliability.
"One of the things that Dynaway is capable of doing is it uses one of our external systems, Fleetwatch, which monitors a lot of our fluid consumption—diesel, coolant, oil, and other fluids —all the type of fluids that a vehicle or a bus needs, as well as mileage. And what that does is it pushes that information that data into the EAM system, and then we're able to utilize that information for repair information, for preventative maintenance information, because, for example, at IndyGo, we do our maintenance every 6,000 miles, so that software will end that mileage counter will increment up to 6,000 miles and it will generate or predict what the next maintenance sequence should be so we can get that maintenance done in a timely manner before there's a breakdown." - explains James.
3. Record Tracking
James highlighted record tracking as another key advantage of Dynaway EAM. He mentioned that several transit companies have approached IndyGo for system comparisons, and the standout difference has been the reporting features:
"When we compare our system with other transit agencies, hands down, our reporting is far better as far as what KPIs we're keeping track of, work orders, process, operation, everything. So that would definitely be one of the things that I share when I talk to other transit agencies."
Collaboration with Dynaway
During our conversation with James, we delved into his experience working with our Dynaway team. He revealed that despite our initial focus on manufacturing and warehouse management, our ability to adapt and tailor our EAM solution was crucial.
We customized the system to meet IndyGo’s unique maintenance requirements, ensuring compliance with FTA standards. This adaptability not only addressed the initial challenges but also established a foundation for a more efficient and effective fleet management system.
"Dynaway has been great as far as if there is an obstacle or an issue pops up, being able to communicate whether it's a ticketing system or emailing one of the guys at Dynaway to get assistance. They've always been readily available and quickly responded back to us, whether it's setting up a meeting to try to identify what the issue is or seeing if there's a better way to do a current process that's already implemented," said James.
Conclusion
In the transportation industry, the use of Enterprise Asset Management (EAM) or Computerized Maintenance Management Systems (CMMS) is not only beneficial but often essential. The maintenance software plays a crucial role in minimizing downtime by efficiently scheduling and tracking maintenance activities, ensuring the vehicles and equipment remain operational and reliable.
Have you ever wondered how much more efficient your transportation business could be with the right maintenance system?
For organizations using Dynamics 365, Dynaway offers a robust solution that can transform maintenance operations. With its flexible mobile platform, seamless integration capabilities, and dedicated customer support, Dynaway is ready to meet the unique needs of any transportation business.