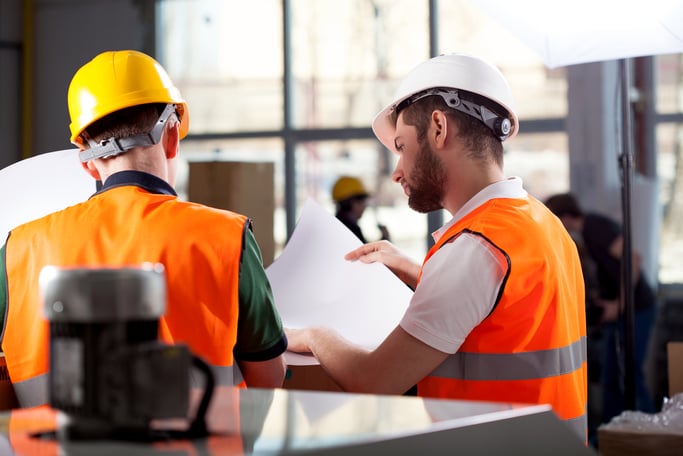
At Dynaway, we rely on proven technologies that help us create great EAM applications and apps. We see our customers as collaborative partners therefore our product development is driven by our customers and users.
Maintenance management is all about optimizing maintenance processes to reduce downtime and overall maintenance costs. However, it cannot be achieved without the right tools! Below you can find a few examples of how Dynaway solves some of the challenges in Maintenance Management like audits, human errors and safety with Mobile Work Order Management Software.
How could Dynaway EAM help manage overtime and audits?
Managing overtime is multifaceted. First because Dynaway tracks labor hours forecasted vs. labor hours actually consumed, you will have visibility when scheduling work to be performed of who has available time in their schedule and if they have the appropriate skills to perform the work. Visibility will give you flexibility.
Secondly, a properly implemented asset management system will enable you to move away from emergency work and toward planned/preventive work. This ensures reliability and reduces overtime due to emergency situations.
Download study document about economic value of preventive maintenance.
The scheduling feature in Dynaway EAM supports granular work order scheduling with visible availability and loading so it is easy to see if you are near overload for any individual and makes it simple to balance the workload on your workers so as to minimize any overtime. Also having a well-documented electronic Worker Order Software can be invaluable in regulatory audits. It gives you the ability to instantly provide proof the work was done, by who, exactly when, and the checks that they performed or didn’t perform to complete the work. In other words, you can have absolutely transparent work order tracking. Having this information instantly for auditors can be a huge advantage and save a vast amount of time and expense.
How can Dynaway EAM assist the mechanics when it comes to their work and human errors?
First, you can have a list of approved spare parts for the machine in question to assure the mechanic understands what parts are valid for the machine. Secondly you can attach file type to the Work Order and have it instantly available on the Mobile Client for the mechanic to review. You might want to include a manual, a step by step word document, a video showing the procedure being done, or anything else that might help. Also, if you prefer, you can include a checklist of step by step instruction that they have to check off to complete the work order. This insures the work is done according to company procedures.
If the checklist you constructed for this job had this step as part of the checklist (perhaps with a video or diagram of how to properly install this) the mechanic would have to check that he performed this step before he could close the work order and enter the parts used and labor consumed. Hopefully this would prompt him to perform the work correctly.
Researching on Mobile EAM functionality? You can find more information about Maintenance Planning, Work Order management and more features here.