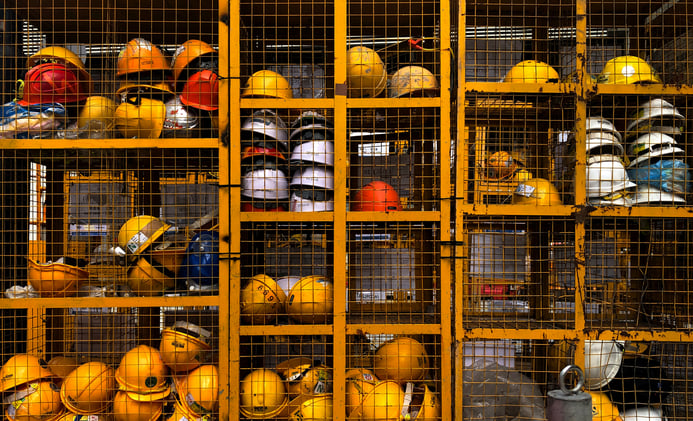
Effective maintenance management helps your business go further by reducing maintenance costs and boosting overall performance.
While minimizing maintenance costs and reducing downtime sometimes are associated with decreasing safety or service, it is actually the opposite. Minimizing maintenance costs is related to efficient maintenance planning and scheduling of work orders which highly increases safety in the work environment and improves the services you deliver to your customers.
How to optimize maintenance?
Nowadays, production companies are taking maintenance more seriously. Companies should prioritize optimizing the level of asset and equipment availability and reliability in order to reduce maintenance costs. When Maintenance Department is completely aware and in charge of equipment and its well being, the cost of maintenance can be highly reduced without affecting the quality of service.
The first step is to identify business areas where technology can render and optimize maintenance processes. Optimal machinery availability is essential even for industries that are not asset-intensive as this determines the success of a business. Customers want to transact with companies that guarantee reliability as they want value for their money.
Well planned maintenance strategy does not mean that you will be spending more money on labor and material costs. It actually enables you to reduce overtime, manpower and spare parts cost. Knowing exactly when and what needs to be maintain, means that you won't have to spend tremendous amounts of time and money on unplanned downtime and reactive maintenance.
Continuous maintenance improvement cycle
Aside from making efforts to reduce maintenance costs and boost efficiency, you also need to have a way of measuring maintenance efficiency as well. You can leverage common techniques and standards to ensure you can coherently evaluate the quality of service delivered. Consider leveraging new technologies related to predictive maintenance so that you know when to conduct maintenance. Your improvement efforts should have high levels of efficiency and effectiveness for you to thrive in today's competitive marketplace. You can find more information about which KPI's to track in order to evaluate Maintenance performance here.
Using advanced analytics or simple reports and dashboards will give you a good understanding about your maintenance costs and department efficiency. Of course, none of it is possible if you do not have a good overview of your data... New EAM/CMMS solutions, enable companies to have data at your fingertips which makes it easier to evaluate and make strategic decisions for improvement.
Have a preventative maintenance strategy
The best way to achieve a competitive advantage in the current scenario of competitiveness is to embrace changes in the industry as they roll in. This way, a company can maximize performance by leveraging innovations and technologies. Consider taking up preventive maintenance as it helps to make sure that your equipment is always in good working order. This proactive approach allows you to prevent asset failure and reduce downtime. Asset failure is not only dangerous for maintenance workers and machine operators, but it will cost you a lot in terms of repair expenses, time to repair and customer satisfaction.
The implementation of advanced technology goes hand in hand with the availability of tools for coherent evaluation. For a maintenance strategy to work, not only do you need to focus on the system but also on process and product. When dealing with the product process aspect, the aim is to establish improvement steps for products. All three should be aligned to maintenance processes for you to achieve success with your preventative maintenance strategy.
Integrated EAM/CMMS solutions enable you to have data and a full overview throughout different departments. For example workers can consume spare parts using mobile devices which will send information to the inventory department and likewise, to procurement department when the level of materials is low.
Read more:7 Reasons Why You Need to Utilize Predictive Maintenance Strategy
Maintenance safety strategy
It is also crucial that you come up with a cost-effective predictive maintenance strategy that's carried out when the machines are running. Getting real-time feedback from your assets allows you to achieve top results in safe maintenance. Since the equipment is often highly complex, even the smallest failures can result in serious accidents. Regular maintenance not only reduces overall maintenance costs but also keeps your equipment and the workplace safe. Inadequate maintenance can easily result in dangerous situations that might lead to health issues or accidents. Therefore it is crucial to monitor the equipment working conditions not only when they are offline but also when they are up and running.
Another fact is that workers tend to make more mistakes under preassure. This is especially accurate if you are using reactive maintenance strategy and you are not aware of your equipment condition. Then, maintaining it becomes quite risky and unsafe because workers are trying to get the equipment up and running as fast as possible and might miss some important details and make mistakes. On the contrary, preventive maintenance strategy suggest to schedule and conduct checkups as well as standard procedures, so maintenance workers have more time to maintain the machinery without stress and follow safety protocol.
Predictive maintenance is an integral part of a safe maintenance environment. Substantial improvements in predictive technologies in recent years allows you to achieve safe and functional work environment. It is essential to carry out predictive maintenance as it ensures that the right tasks are executed to curb workplace accidents. This way, performance does not drop, and ultimately, maintenance costs do not increase.
Balancing budget allocation with asset maintenance
Even with the pressure to reduce maintenance cost, companies should prioritize safety and service as well. Below are questions maintenance managers should consider asking themselves to ascertain balance between budget allocation and asset maintenance;
- Are you in a position to meet performance targets with your budget allocation?
- Is it possible to reduce the reactive work volume?
- Can you identify key cost drivers?
- Does your line of sight allow you to see documented failure models, maintenance tasks risks?
Companies need to ensure that assets and budget deliver performance targets. A gap between the budgeting process and performance target setting can cause a company huge losses. It is possible to reduce your budget and maintain or improve performance when you effectively evaluate companys' requirements. With proper budget, assets can positively impact on cost and performance.
Cost position allows you to asses budget spend to ensure that the most cost-effective tasks are in place. Even though high-cost assets tend to be informally understood because actual numbers are hard to come by, proper communication and data evaluation allow a company to come up with defensible budgets.
Aside from cost position, companies can also leverage asset assessment to develop cost justified tasks. Normally, the initial assessment acts as the baseline for dynamic budgeting. When real data drives the budgeting process, companies can achieve optimization that not only prioritizes safety and service but also reduces costs.
Conclusion
Even with the pressure on companies in asset-intensive industries to reduce maintenance costs, it is important to ensure that the safety of the workplace and service delivery is not sacrificed. Coming up with the right strategies allows you to achieve your objectives and improve company performance.
Instead of reducing maintenance work hours, or quality of tools and spare parts which therefore immediately affect quality of maintenance, equipment, safety and overall company performance, we suggest another, cost efficient approach!
Such vital changes can be done with the implementation of tried and tested technologies and strategies. Consider learning more about EAM's built-in enterprise asset management software that is certified for Microsoft Dynamics. This software can seamlessly be integrated into your operations to boost work-order execution.
Interested in saving money on Maintenance Costs?
You can access more useful resources and research papers here.