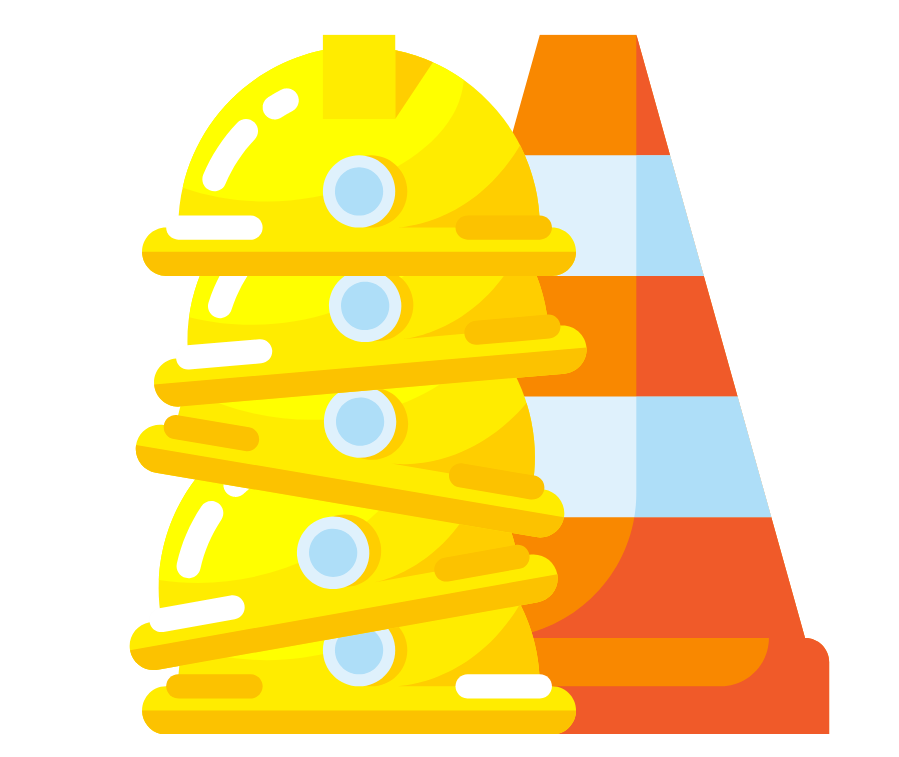
Dynaway Safe Work helps you improve and digitize your safety processes and align them with maintenance activities.
Screenshots
Features
-
Risk Assessment
Create and manage Risk Assessments
Risk Assessment is used to identify and mitigate the risks involved in maintenance work:
- Identify the hazards that could impact maintenance work in a negative way.
- Calculate a risk value for each hazard.
- Add the precautions required to mitigate or eliminate the hazards.
- Identify the hazards that could impact maintenance work in a negative way.
-
Lockouts
Create and manage Lockouts on Assets and Work Orders
Lockouts are records created to ensure a safe work environment.
A Lockout contains a list of Lockout Points that stops the energy in a work area, so it becomes safe to carry out a work order.
The worker has to follow a written procedure for the lockout and test the lockout before the work order is executed and re-instantiating the equipment once the work order has been completed. -
Tagouts
Create and manage Tagouts on Assets, Work Orders, and Locations
A Tagout is a safety measure to ensure that maintenance work can be carried out in a safe way.
Tagout examples:
- Place barriers around a work area to restrict access
- Block access to high-energy sources
-
Permit-to-Work
Digital Permit-to-Work Management System
Permit-to-Work is a written safety control system used to help prevent accidents or injury to employees and prevent damage to equipment.
Work Order Permits ensure that work is evaluated and approved before it gets done – and that the worker is informed, trained, and supervised to minimize the risk of any potential mechanical, technical or human failure events from occurring.
A work permit describes conditions to be met, and safety tasks to be done. The permit is related to a work order to ensure that the conditions or tasks described in the permit are solved before work is started. -
Inspections
In EAM-BC you can work with Rounds to plan and carry out the same job on multiple Assets in one Round Order. In the Safe Work module, we have extended this functionality to allow you to add Checklists to your Inspection Rounds.
A Checklist contains a list of tasks (lines) to be completed in sequential order before, during, or after the inspection job described in the Round Order. You can add three checklists to a Round Order:
- Before Round - this checklist contains tasks to be done before you start working on the inspection job on each Asset included in the Round Order.
- After Round - this checklist contains tasks to be done after you have completed the inspection job on each Asset included in the Round Order.
- Each Round Step - this checklist contains tasks to be done on each Asset as part of the inspection job described in the Round Order.