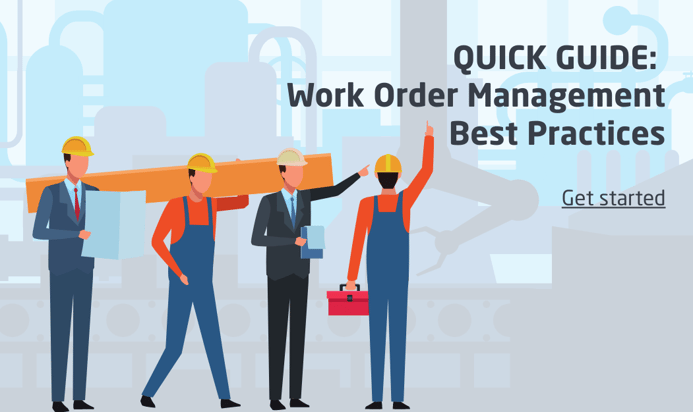
Work order management.
If you do it the right way, your organization will reap the benefits. It will witness a transformation in productivity, maintenance effectiveness and decision-making.
And that translates to lower Operations and Maintenance costs, better ROI for your EAM or CMMS investment, and more *SMFs around the offices. (*Smiling Management Faces)
OK, that’s enough acronyms from the world of M&R.
That last one slipped out. Old habits die hard.
Anyhow before we get to the right way to do work order management…
What is a work order?
It’s a maintenance document, plain and simple.
Whether paper or digital – the work order (WO) shows all the information regarding the lifecycle of a maintenance task for planned and unplanned work. It will include who requested what work on what asset (service request) and its priority; the planning information in terms of the work to be done, labor, parts, tools, estimates; and work feedback for work performed, the delays and the problems.
It’s often split into three broad sections:
- Requester section
- Planning section
- Feedback section
The information comes from three sources: the requester or originator (usually the asset operator), the planner, and the work completer (technicians, engineers, etc.)
We said that it’s a paper or digital document earlier.
Strictly speaking, that’s not always the case…
The different types of work orders
If you put your hard hat, boots, and hi-vis vest on and went out into the world and did a tour of random plants, then these are the types of work orders you’d likely see:
- Pen & paper
- Whiteboards, marker pens and sticky notes
- Computer spreadsheets
- EAM/CMMS (PC-based only)
- EAM/CMMS (Cloud-based & mobile)
Let’s look into each individually.
Pen & paper:
The work order was born this way in decades gone by, and it may still work well for smaller operations. You see, people are comfortable handling pens and paper. It feels real. Tactile. However, it has many drawbacks. Work orders will be slow and inefficient to process. They can be lost, damaged, and bulky. Some would say a fire hazard. Your planner’s scribble may be illegible to technicians. ‘Repair the seal’ may look like ‘Repaint the seat’. Explain that one to management when things go wrong.
And paper can give you a slicing, painful papercut. Ouch!
Whiteboards, marker pens and sticky notes:
It’s highly visible, available, and easy to access (if your desk is near it). But lots of disadvantages as you’ve guessed. Difficult to impossible for storing work history; work orders will be slow to update; and everyone must go to the board to raise or close WOs. There’s no automatic triggering of WOs of course. And just like with pen and paper, trying to find and analyze historical work orders for a reliability project is an easy way to an instant headache.
And… sticky notes fall off easy, and then get trampled with oily boots.
Computer spreadsheets:
Now we’re into the computer domain. At last! But don’t get your hopes up just yet. Of course, WOs are now digital and so are less prone to being lost, crumpled, or suffer water or fire damage. And they can relatively easily be analyzed for data and turned into information reports. But! They don’t update or trigger WOs automatically. If they are not cloud-based, they may be locked onto one person’s computer or cumbersome to update.
A step in the right direction, but still old school.
EAM/CMMS (PC-based only):
Now we’re getting somewhere.
Sometimes known as EAM (enterprise asset management) or CMMS (computerized maintenance management system). This type of software allows everyone easy access to work orders because it resides on the organization’s network. Like spreadsheets, it’s digital. Reports are easy to generate on costs and resources. However, some traditional systems can be very expensive and cumbersome to implement and use. When they are PC-based, most organizations still rely on printing out work orders and taking them to the jobsite. Widespread training is also required for EAM/CMMS and often there is cultural pushback with the less intuitive systems.
EAM/CMMS (Cloud-based & mobile):
Digitalization and connectivity.
All work order tasks can be created, planned, tracked, closed, and analyzed in real time from anywhere: in the office, on plant, in the canteen. It’s always up to date and is a source of maintenance and business intelligence and operational efficiency. The work order can be influenced by anyone with access to a PC, laptop, phone, or tablet. The benefits and value provided are significant. Automatic triggering of PMs. Images of the failed components added to the WO. Real time status tracking. Easy access to asset history, WOs, manuals at the site of work. The list goes on.
What’s there not to love?
Work order management
Work orders are used for both planned and reactive (unplanned) work.
Planned WOs are usually for scheduled preventive maintenance or corrective maintenance that comes from inspections. Condition monitoring inspections are also planned. Reactive WOs will come from breakdowns, i.e. the unplanned painful ones that cause headaches and anxiety from shop floor to top floor.
Like everything else concerned with maintenance, WOs must be managed.
When we say work order management, this is what we mean:
|
So, we must manage work orders. But why?
What are the benefits of good work order management?
Higher operational efficiency – Modern WO management solutions allow for a reduction of errors. Real-time dashboards deliver insights for the organization that can be acted upon quickly. Automation provide phenomenal leverage.
Better employee productivity – technicians will spend less time at their desks because of mobile solutions, modern work order management, and well-planned tasks. Better insights into wrench time can also be gained through WOs.
Effectiveness – when WOs are planned correctly - work task steps, correct resources, correct tools – maintenance will be right first time.
Improved decision making - data-driven decisions can be backed up by reports and analytics from the EAM or CMMS.
Higher asset availability – WOs allow for proper planning and scheduling of the right maintenance at the right time. When this is done right, you get shorter maintenance downtime periods and that means higher asset availability.