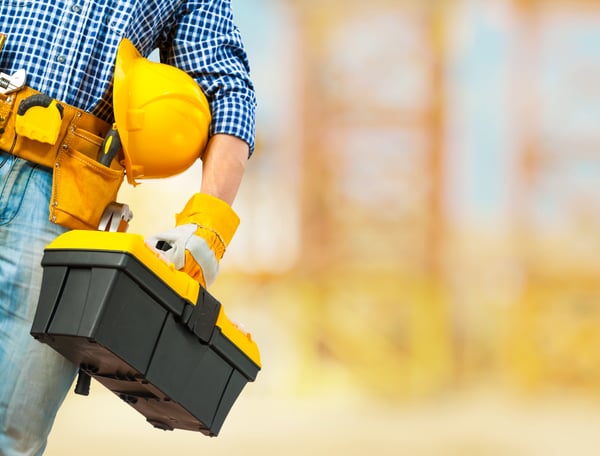
Adopting a preventive maintenance model for your facility and practicing its tenets according to a regular routine can boost your company's overall production, keep equipment running at an ideal level and alleviate downtime. Total productive maintenance (TPM) is among the most popular methods used to achieve such goals: The approach is highly focused on employee empowerment, and helps guarantee greater availability, performance and quality.
- Total productive maintenance (TPM) is a method used to boost the company's production, equipment efficiency by minimizing downtime.
- By implementing the TPM strategy, it's possible to see maintenance costs drop 25-30% and conversion costs decline by 20-25% over five years.
- Among major benefits of TPM process are safe work environment, a proven impact on efficiency, improvements to overall staff morale and increased customer satisfaction.
- Condition-based maintenance is similar to TPM, but achieves its continuous monitoring of equipment through implementation and leveraging of industrial internet of things (IIoT) frameworks.
Performance is optimized by minimizing the likelihood of breakdowns and ensuring that operational slowdowns or pauses are as infrequent as possible. This, in turn, significantly reduces the chance of product defects, which can help improve the quality of your finished goods. Also, implementing the TPM strategy can realize notable cost savings over time by boosting overall equipment efficiency: According to Mark Jolley, director of manufacturing services at the Marshall Institute consultancy, it's possible to see maintenance costs drop 25-30% and conversion costs decline by 20-25% over five years.
Here, we'll explore what TPM actually involves, and also take a closer look at how it benefits manufacturers, food service companies, energy providers and firms from various other heavy industrial sectors.
The fundamentals of total productive maintenance
At its core, the TPM approach is about the maximization of productivity — as well as the lifespan of equipment — by allowing workers to take more responsibility for these issues on a day-to-day basis. This is achieved in the following ways:
1. Autonomous maintenance
TPM assigns the responsibilities for routine equipment maintenance tasks, such as lubrication, cleaning and inspection, to the regular operators of various machines throughout the facility. Workers thus cannot simply let their equipment fall into disrepair or otherwise bad shape, relying on the intervention of dedicated maintenance technicians to bring it back to working order. (Think of it this way: If they were to take that lackadaisical approach, what do you get when maintenance staff are unavailable for any reason? Unplanned downtime, which no business can afford for long — or, in some cases, at all.)
There are many benefits to this proactive maintenance technique. For one, maintenance staff have more time to deal with higher-level duties — namely, addressing truly unexpected and urgent production equipment failures. But while operators may initially be less than enthusiastic about having more responsibilities on their plate, the TPM process increases their degree of familiarity with the equipment over time, and that makes their jobs easier in the long run. It also ensures that these employees are better equipped to identify any small issues with the machinery as they emerge and address them without having to bring the maintenance team into the picture.
2. An ongoing strategy of planned maintenance
TPM typically involves the scheduling of maintenance tasks based on measured and/or predicted failure rates. This reduces instances of unplanned stoppage, allows for equipment to be serviced during off-work hours and cuts down on inventory (through enhanced control of both failure-prone and wear-prone parts). In this sense, it is the antithesis of reactive maintenance, where repairs are only made when absolutely necessary — usually because of total or near-catastrophic failure of a machine or system.
3. Quality maintenance
Implementing a TPM strategy can help an organization incorporate error detection and prevention practices into the overall production cycle. This stems from the methodology's basis in the principles of root cause analysis (RCA): Looking at maintenance from an RCA perspective eschews examination of simple cause-and-effect dynamics in the interest of tracking down exactly how a process, system or device failed. Doing so better equips workers to determine the most effective response to a problem.
Because an RCA-based TPM framework usually focuses on eliminating the causes of defects that lead to equipment malfunction or failure, it slowly but surely improves the quality of various operations. Furthermore, it helps cut down on costs by increasing the chances that faults are uncovered early on, before they can do too much damage and necessitate expensive repair or replacement tasks.
4. The drive for focused improvement
This aspect of TPM is about having smaller groups of staff working together proactively toward achieving systematic, incremental improvements in machine operation. As such, you avoid having individuals stuck with the sole responsibility of keeping things running smoothly with their equipment and the chaos that results from having "too many cooks in the kitchen."
Here, small but cross-functional teams can identify and resolve recurring problems. It also combines a pool of talent within the company, and this further catalyzes continuous improvement.
5. Early equipment management
The understanding and practical knowledge of processing machines gained through the TPM approach is directed toward the improvement and designing of new equipment in this principle. Because there are fewer startup issues when TPM is properly implemented and executed, new machinery could reach its ideal performance level more quickly. Additionally, equipment servicing and other maintenance activity is much easier and more robust as a result of employee involvement and practical review before installation.
6. Education and training
TPM is dependent on filling any knowledge gaps that prevent your business from achieving key maintenance goals. This applies to managers, maintenance personnel and operators alike:
- Managers train on TPM principles alongside their subordinate, lateral and superior staff. This helps them better understand how stakeholders across the organization deal with maintenance issues from their distinct vantage points.
- Maintenance personnel perfects the techniques necessary for the proper execution of proactive and preventive equipment management strategies.
7. Safety and health
Maintaining a healthy and safe work environment should be a key concern for any company where heavy machinery (or other equipment that can be dangerous outside of its proper operating context) is required on a regular basis. Doing so is in the best interest of both simple human decency and the complexities of regulatory compliance.
TPM puts these concerns front and center. It helps eliminate potential ongoing safety and health risks while also minimizing the possibility of sudden and catastrophic accidents.
8. TPM in administration
This fundamental involves the application of TPM techniques to the company's administrative functions. It extends the benefits of the approach beyond the factory floor of the facility by addressing any time or effort that is wasted in the course of executive and managerial operations. Adopting these principles can be especially important for improving procurement, scheduling, order processing and asset management.
Major benefits of the TPM process
By involving operators in the performance of maintenance tasks — and planning and scheduling such activities to ensure consistent oversight of key equipment — your organization has the potential to realize the following benefits:
1. Safer work environments
In addition to frameworks like RCA, TPM is also based on the structured management system commonly known as the 5-S method for its alliterative steps: Sorting, Setting in order, Shining, Standardizing and Sustaining.
All of the S's point to the idea that keeping equipment and machinery clean, organized and healthy could improve safety in the work environment. The focus of TPM on proactive and preventative servicing increases the lifespan of equipment while also cutting on workplace disorderliness. It also facilitates designs that maximize productivity, efficiency and flow. All of these qualities form the basis of safety for workers at all levels.
2. A proven impact on efficiency
The major goal of the TPM approach is achieving a condition sometimes referred to as "perfect production." In other words, any manufacturer considering TPM aims to achieve zero defects, breakdowns or accidents. This means you may have to focus on quality over quantity while also prioritizing efficiency over output.
You can measure TPM using the Overall Equipment Effectiveness (OEE) grading scale — generally thought of as the gold standard for quantifying productivity in the manufacturing process. The rating applies to both process and discrete production settings. It facilitates improvement by quickly identifying any loss areas, comparing progress and improving equipment productivity — all with the foundation of comprehensive data. Solid metrics speak volumes, and with OEE, you can benchmark the facility against industry standards and confirm whether the TPM improvement program you are using is working.
3. Improvements to overall staff morale
To fully implement lean manufacturing, you need employees across your entire organization at all levels to buy into the idea wholeheartedly. If it presents positive results, staff may be less likely to inherently resist the changes.
TPM is similar in many ways: Through its principles, employees are empowered with the responsibility to take care of their equipment. Consequently, they may tend to take pride and ownership in their work. The preventive steps inherent to TPM result in fewer cases of equipment failure and a minimum of frustrating downtime. These successes will only increase your employees' commitment to the TPM philosophy.
4. Increased customer satisfaction
A safe workplace, employee morale and efficient production are all major perks of productive maintenance. However, many would argue that customer experience and satisfaction are even more important in the long run. The TPM pillar of quality maintenance allows for the integration of quality improvements into the production process. As a result, there is usually a reduction in reworks and defects and an increase in output and quality. This, coupled with reliable machines that experience less downtime, can help lead to an increase in satisfied customers and repeat business.
Is a TPM program ideal for your business?
Very little is cut and dried in the various manufacturing and industrial sectors, and every company is different. Although TPM can be beneficial to any company in theory, it might not be the perfect system for your organization in practice. It may perhaps be worth your while to implement it on a smaller scale, or as a pilot program, and observe the results for a finite period (several months or so) before committing to it as a permanent solution.
Condition-based maintenance is similar to TPM, but achieves its continuous monitoring of equipment through implementation and leveraging of industrial internet of things (IIoT) frameworks. This may be preferable if you feel more comfortable assigning the oversight of equipment efficiency to cutting-edge (and entirely objective) technology. That said, like TPM, it can be costly to implement, and maintaining it is also not cheap. If you're truly strapped for cash, it may even be necessary to stick to a reactive model for the time being — while keeping TPM in mind as a system to aspire to.
How do you devise the best maintenance strategy for your equipment?
You may also want to consider not choosing one specific maintenance model over others: Instead, you could combine elements of multiple methods, creating a unique model for your organization's specific needs. For example, it wouldn't be unreasonable to take a reactive approach for equipment that is low-priority or has diminished breakdown risk. At the same time, you'd have your operators take a hands-on ownership approach to critical operational technology such as your industrial control system (ICS). This diversity of styles would take time for employees to grow accustomed to it, so proceeding gradually is best.
Productive maintenance — whether in the TPM framework or in another format — aims to improve the reliability of equipment by inspiring employees to take pride in its upkeep. If done well, the approach can bring about measurable, lasting benefits such as proactive company culture, reduced turnover, improved quality output and greater customer satisfaction.