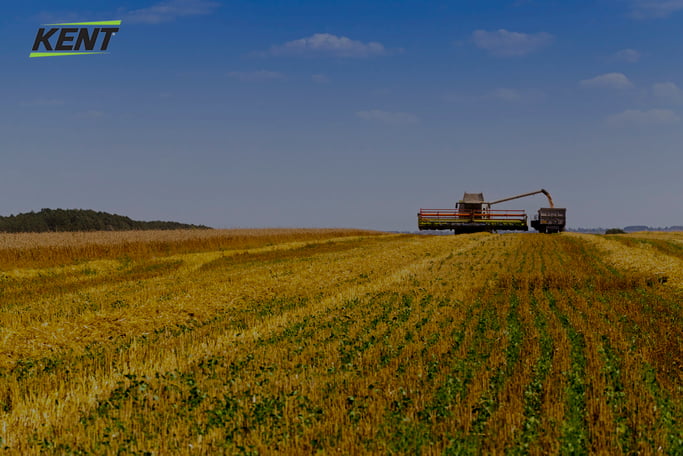
Dynaway EAM reduces reactive work orders by two-thirds – and counting – at Kent Corporation
At a glance
THE CUSTOMER: Kent Corporation – a leading food and feed manufacturer
Kent Corporation is a diversified, family owned corporation with operating subsidiaries involved in corn wet milling, the production of animal feeds, and the manufacture of food products. The entire family of companies has approximately 1,800 employees and does business in the US, Canada, and throughout the world.
THE CHALLENGE: Efficiency, cost-control and easy access to information were lacking
An antiquated maintenance and spare parts system made it next to impossible to retrieve information, slowed down work processes, and led to reactive maintenance, rather than proactive maintenance.
THE SOLUTION: Implementation of Dynaway Enterprise Asset Management (EAM)
Dynaway EAM and the Dynaway Mobile EAM Client have been integrated with Kent Corporation’s new Microsoft Dynamics AX solution in two of their 22 plants, with the rest to follow starting in 2018.
THE BENEFITS: Increased efficiency, ability to act proactively, improved access to information
• Reactive work orders down by 60%
• Overdue work orders halved
• Improved performance and less downtime
• Fast access to data on performance and costs
• More efficient planning
• Simplified compliance – successfully passed outside audits
Dynaway EAM helps top food and feed manufacturer move from inefficiency to effectiveness in ten short months.
Learn how Kent Corporation went from stacks of printed work orders, hours-long planning sessions and bespoke queries each time they needed to access data from their system, to sound planning, and having information at their fingertips.
One comprehensive platform for everything
“The system we were using was a dinosaur,” says, Matt Conard, Business Process Lead at Kent Corporation. “Our work orders were printed on slips of paper, and there was no good way to keep track of which ones were closed and which were still open. If something got lost, it was gone forever. And it was difficult to get information out of the system. It was clearly time for a change.”
Kent Corporation was in the midst of a company-wide migration to Microsoft Dynamics AX. The original plan was to retain their old maintenance and spare parts system and integrate it with the new solution. But the old system, though state-of-the-art when implemented, was not serving their needs for efficiency, cost-control and, in particular, easy access to information. So the decision was made to implement a new Enterprise Asset Management (EAM) system to extend their Microsoft Dynamics AX platform. Kent Corporation found Dynaway, and it has been smooth sailing ever since.
The right partner, with the right solution
“It’s always been an easy conversation with Dynaway,” says Conard. “The team was quick to respond, and was receptive to our needs from the beginning. And they’ve proven themselves to be equally responsive throughout the entire implementation project.”
Kent Corporation went through a long vetting process, looking at a number of other prospective partners. But the products they saw were more costly and required more setup, and the suppliers were slower on the uptake. The maintenance workers and supervisors who tested the Dynaway solution all agreed it was simpler and more straightforward. It would be easier for users to learn. And – just as important – the partnership simply felt right.
The quickest, most successful go-live
Dynaway worked with Kent Corporation to implement a solution that supports the company’s internal processes and to help them make the switch as quickly and painlessly as possible. Workshops were held with representatives and power users from IT, Finance, Maintenance, and Warehousing. They provided input to Dynaway, and Dynaway trained the people who would go on to train their colleagues. The next few months were spent converting and cleaning data from the legacy system, and by the second series of workshops, the environment was up and running. The following months were focused on data conversion and tweaking the solution to suit Kent Corporation’s needs before the solution went live.
“This is a partnership,” says Conard. “We have our own in-house development, but we’ve still relied on Dynaway for customization, advice, and training. They’re so knowledgeable, and really good at listening. And I have to say, Dynaway delivered the quickest, most success-ful go-live I’ve experienced.”
Learn more about Dynaway Implementation Services
No more time or money lost “sitting around” in meeting rooms
It used to be quite a challenge for Kent Corporation to take advantage of planned outages to complete work orders on all the assets involved in the outage. Super-intendents and maintenance staff had to check hand-written notes and trudge through piles of work orders to figure out what work there was to do.
“With Dynaway EAM,” says Conard, “the information we need is easy to access. We filter on the outage, and all the work orders are right there. We can prepare and move on. No more time, and money, wasted sitting around in meeting rooms planning. And we don’t miss anything.”
Cost transparency and seamless integration
In addition, Conard points out that they can now link purchase orders to objects via a work order, which means they can track costs directly back to the objects instead of just to the department. And that seamless integration with the Warehouse and Procurement modules in Microsoft Dynamics AX let them easily check availability of parts and order what they need via the system.
From putting out fires to preventing them Maintenance manager Walker has been with Kent Corporation for 19 years at their corn milling plant. With a staff of 60 employees, and contractors reporting to him, one of Brian’s primary goals was to change the way his people worked to go from reacting to issues as they occur, to acting proactively.
“I wanted to stop putting out fires and start preventing them, and we’re doing it,” says Walker. “Tools that increase accountability and help us understand what’s getting done, what’s not getting done, and whether we’re staffing correctly, have helped us cut reactive work orders by two-thirds. And that’s an ongoing trend. The result is more reliable assets, much less unplanned downtime and higher productivity.”
Everybody got right onboard
“Another thing, I’m happy about is how fast people have gotten on board and how enthusiastic they are,” Walker continues. “My superintendents are excited because now we can gauge our success. They can see where we’re doing a good job and where we need to make an extra effort. They can look at the KPIs and share results with their own teams.”
The new transparency enabled by Dynaway EAM has been great for everyone’s morale and motivation – from supervisors, to hourly staff, to contractors. People are intrigued and inspired by the insights and hands-on results they have had access to since go-live.
The biggest benefits are just starting to emerge
Natalie Oppel, Business Architect in Kent Corporation’s IT department says the configuration options available in Dynaway EAM that allow them to look at different types of work orders and group things will in the long run allow the company to see how they’re spending their money:
“Where are the biggest equipment costs? Which five assets are costing us the most? How do costs compare across plants? We’ve been able to design and configure the solution in a way that will help us get data out in a meaningful way. That’s where the biggest benefits lie,” says Oppel.
Efficiency, savings and access to valuable information
So far, Kent Corporation has implemented Dynaway EAM at two of their 22 production plants, which account for around 20,000 assets. Over 500 people are currently using the solution. In 2018, the company will start the process of rolling out the new solution at the remaining plants. They plan to implement Dynaway EAM at their other plants in exactly the same way as they did at the first two.
“We’ll start by bringing Dynaway in for a workshop and then bring them back every six months to help us get even more out of the solution. That approach has worked so well for us,” says Matt Conard. “We fully expect to realize the same benefits in terms of efficiency, savings and improved access to valuable information.”