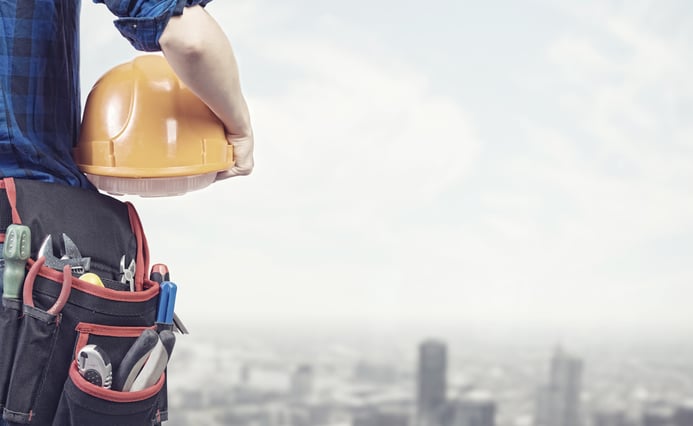
Maintenance is essential to the steady long-term operation of any factory, industrial site or other, similar organization.
- Preventive maintenance is a form of proactive maintenance — regularly scheduling maintenance activities before a piece of equipment malfunctions or exhibits notable problems.
- We can distinguish five maintenance strategies within preventive maintenance: time-based maintenance, failure finding maintenance, risk-based maintenance, condition-based maintenance and predictive maintenance.
- Among the benefits of preventive maintenance are: extending life of assets, preventing the need of major repairs, preventing delays and more.
As far as today's equipment and machinery have come, they nonetheless face the same threats of decline and depredation over time that they always have: The only real difference between then and now is that improvements in component and raw material manufacturing — and advances in methods of maintenance — have helped extend the life cycles of parts, machinery and overall systems.
Preventive maintenance (PM) is among the most effective modern maintenance strategies, offering distinct advantages over less thorough and more rudimentary methods. Today, we'll take a comprehensive deep dive into the essential tenets of a preventive maintenance program, while also looking closely at the best attributes of maintenance software most appropriate for the preventive framework.
What is preventive maintenance (and why is it important)?
Preventive maintenance is a form of proactive maintenance — e.g., making repairs before a piece of equipment malfunctions or exhibits notable problems — that is performed regularly at predetermined intervals to prevent asset failure and unplanned downtime. As such, a preventive maintenance program is a critical part of maintaining any business's assets as it ensures optimal equipment performance in the long term. In fact, properly caring for the health of your company's vital assets can help to not only reduce the costs of equipment maintenance but also help cut down on more general bottom-line expenses for your organization.
If your business has been relying on reactive maintenance for your equipment and only attempting to repair or replace after significant failures or malfunctions, it could be well worth your time to consider switching to a preventive maintenance strategy. Although the reactive model is sometimes cited for its cost-savings due to the expense associated with implementing a preventive framework and because of lower direct maintenance costs, relying solely on need-based maintenance could likely mean that costly repairs or replacements add up to much more than any upkeep costs of a preventive model.
What are the key types of preventive maintenance?
According to Road to Reliability, there are five distinct types of maintenance strategies that fall under the umbrella of preventive maintenance.
- Time-based maintenance (TBM): If following this strategy, members of your organization's maintenance team would update or replace a given component, device or piece of equipment at specific intervals determined by a fixed schedule. It does not matter whether the item in question actually needed to be fixed or swapped out — the schedule is meant to be followed to the letter. (To be fair, scheduling is typically formulated with component and equipment life cycles in mind, but it still remains something of an inexact science.)
- Failure-finding maintenance (FFM): FFM is a particularly niche branch of the PM tree. It involves tracking down failures that affect protective components such as trip transmitters or pressure safety valves. You will not know that they've failed until the problem they're supposed to ameliorate isn't mitigated (leading to another separate failure). FFM is conducted according to a fixed schedule that may be determined through risk analysis or another, similar method.
- Risk-based maintenance (RBM): Risk analysis plays a prominent role in countless aspects of business, so it's no surprise that it found its way into the core tenets of a preventive maintenance operation. In this variation on PM, equipment that has both a high risk of failure and poses the gravest consequences when that failure occurs will be examined and maintained more often than any other machinery, devices or components. By contrast, low-risk equipment is maintained with much less frequency. Using the basic risk = likelihood x consequence equation as well as other more specific methodologies, RBM functions as an economically sound form of preventive maintenance service.
- Condition-based maintenance (CBM): This type of maintenance activity takes place at variable intervals — specifically, it occurs based on the measured health of any piece of equipment or other critical assets. A maintenance technician would not necessarily be looking for obvious problems, but instead might focus on subtle signs of distress: the sort of things that don't add up to much now but could quickly turn into serious trouble. CBM may sometimes be implemented in conjunction with sensors and gauges connected to the industrial internet of things (IIoT). The intention is to minimize downtime and cut down on the costs associated with full-fledged repair or replacement after a catastrophic equipment failure.
- Predictive maintenance: This iteration of preventive maintenance is a spin on CBM, with the added dimension of the machine-learning frameworks found in the most advanced artificial intelligence deployments. Because AI is still very much in its nascent stages, predictive maintenance is hardly the most common variant of the preventive family, but that certainly could change in the not-too-distant future. (Many types of preventive maintenance software feature sophisticated automation; it's only a matter of time before that automation becomes a type of AI.)
All of these variations on preventive maintenance can be useful. But you will have to think carefully about which is best for your unique situation, rather than simply choosing the type with the most obvious perks.
What are the benefits of preventive maintenance?
A maintenance strategy that is proactive and preventive in the most ideal way offers too many benefits to enumerate line by line in a simple list — so we instead focused on six broad factors that can stand in for many others.
1. Help prevent the need for major repairs
Implementing preventive maintenance can significantly aid in your efforts to prevent the need for untimely major repairs. By using software programs like computerized maintenance management systems, routine preventative maintenance schedules will lead to fewer major maintenance operations on your equipment. The fact of the matter is: All of the faults and small failures found in equipment and other assets will get worse over time — it's simple physics, really — and the longer an issue goes unfixed, the more damage it can cause.
Relying on reactive maintenance, as opposed to a preventive model, will result in performing maintenance less frequently. This could create useful savings in the short term. However, doing so will likely also result in your equipment breaking down and requiring costly, complex repairs. It can be quite frustrating to have your equipment fail only to find out that what could have required a simple fix a month or so ago is now a significant problem requiring immediate intervention. Preventive maintenance allows you to address small issues over time, which in turn can help prevent major problems and make maintenance less expensive — and easier to handle — in the long run.
2. Extend the life of assets
When equipment is neglected and not properly maintained, this drastically reduces its life span. While some will neglect proper maintenance thinking that they're saving money, in truth it can easily have an opposite effect. The time and money you invest in maintaining your equipment will extend its life, and that saves you a great deal of money in the long run by limiting the number of times you must shell out funds for repairs or replacement.
3. Reduce maintenance costs
There's a serious misconception about preventive maintenance: namely, that it will cost much more money than the value of the corrective action. In fact, proactive, preventive maintenance generally has the opposite effect: Catching small issues before they turn into major problems can save you the expenses of major repairs down the road, potentially lowering overall equipment maintenance costs. Investing in regular, low-cost maintenance and repairs can help ensure that your equipment does not require more expensive repairs down the road or necessitate the exorbitant cost of replacement. Also, conducting regular preventive inspection operations will aid in your inventory optimization, by minimizing the amount of capital put toward equipment inventory while still maintaining an appropriate level of service.
4. Prevent delays
Relying on reactive maintenance instead of investing in a preventive maintenance plan can cause costly delays and reductions in productivity. Should you wait until an asset shows signs of problems or breaks down altogether, before you perform necessary maintenance, you may find that a crucial piece of equipment has become unusable for a significant period of time. This can mean a substantial drop in productivity, which could result in significant delays, loss of contracts, and a dip in revenue. Therefore, despite the early expenses involved in implementing a preventive maintenance strategy, it should still be viewed as a cost-saving investment in your company's future stability.
5. Increase Productivity
Not only can unexpected breakdowns cause decreases in productivity, but a lack of regular maintenance can also cause your equipment to slow down over time. After continual use, all equipment and devices will begin to deteriorate in functionality, making them less efficient and more unreliable. Although the deterioration usually proceeds slowly enough that you will not quickly see any significant changes to the equipment itself, there will be a drop on the device's performance or production sooner rather than later.
Much of this deterioration can be avoided by investing in a proper preventive maintenance plan. By taking proper care of your equipment, you can slow down the march of deterioration and help maximize the productivity of each and every asset at your disposal.
6. Enhance Safety
Equipment failure and malfunction can lead not only to expensive repairs but also to safety issues that could grievously harm you or your employees. For instance, should a worn hose that pumps hazardous materials suddenly fail, this could seriously injure a nearby operator. This would not only cause damage to facilities and halt production but could also leave you liable in lawsuits brought against you by employees due to your negligence. Preventive maintenance is thus a necessity for helping to ensure the safety and efficiency of your work environment.
What are the cons of preventive maintenance?
A preventive strategy can come with its drawbacks. It will usually cost more to implement preventive maintenance as a core strategy than it will to have reactive maintenance protocols on the back burner that only engage when something goes wrong. This is especially true if you pay for an advanced network of IIoT-enabled sensors and similar components to create a condition-based maintenance policy. Also, a preventive strategy implemented according to the time- or failure-finding models may not be appropriate for all organizations, and managing preventive maintenance work orders may be quite time-consuming.
However, everything we've gone through in the previous sections should serve as an effective summary of preventive maintenance's benefits, particularly in contrast to reactive or corrective maintenance. Any steep short-term investments will be well worth the long-term gain.
Who should use preventive maintenance?
Adopting a preventive maintenance strategy would be especially appropriate for any organization that must meet many strict regulatory requirements. Just about every heavy manufacturing company falls into this category, as do energy and petrochemical businesses, hospitals, urban construction firms and any other facility-based organization that will suffer from unscheduled downtime and loss of revenue.
According to a recent study by ServiceMax, more than 80% of the 600+ companies responding to the research effort said they'd experienced unexpected downtime resulting from an equipment failure during the last three years. Maybe that isn't true of your organization, but regardless, issues of this kind are far more common than you might think.
How can you plan a preventive maintenance strategy?
A question like this has countless answers. In the early stages, it will be more a matter of setting aside the time for a small maintenance task here and there: repairing an item that's only slightly malfunctioning but shows signs that it might fail more severely soon, swapping out terminals at employee workstations and so on.
As you progress, you and your team will likely see more opportunities to preemptively fix or replace key issues. However, planning a preventive maintenance schedule and determining when and what needs to be done can be extremely difficult. You will have to track data manually to determine when servicing needs to be performed based on time and usage data.
This is where an enterprise asset management (EAM) tool like Dynaway can prove essential: The solution can help you plan, track, and optimize your maintenance activities, and also help ensure maintenance is performed as necessary to keep equipment running at optimal levels. At first you may be surprised how easy it makes daily tasks for you, your maintenance manager and the rest of your team, but soon it'll become part of your organization's essential fabric.