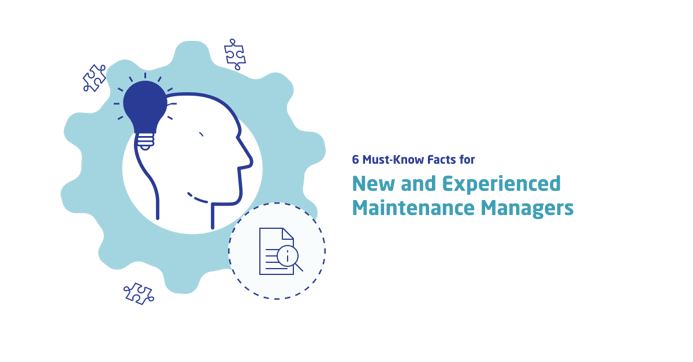
The role of a maintenance manager might be compared to being a soccer club manager: you are facing pressure from all angles - from below, from above, and from the sides.
You’re a strategist and a tactician.
Results - good or bad - come back to you. And sometimes unfairly so.
But the pressures can be managed and used for good if you understand what they are.
- As a maintenance manager, you must be prepared for facing many challenges such as managing KPIs, risk management, maintenance planning, and communication with multiple stakeholders including your maintenance team, operations, IT department, and others.
- Highlighting the long-term benefits of maintenance as a factor that adds value to all parties involved, can help you improve communication throughout the organization.
- Applying documented risk management frameworks, such as ISO 31000, will enable you to assess and analyze risks more efficiently.
- CMMS/EAM is a good tool for planning and scheduling maintenance work.
- Delegating tasks will not only reduce your stress but also provide others with leadership opportunities, increased motivation, and higher job satisfaction.
What Pressures?
In any managerial role, every day will be a challenging mix of meetings, targets, deadlines, KPIs, conversations, cold coffee, and waiting for Zack from IT to finally set up your remote access portal.
Maintenance management is no different.
You’ll have multiple stakeholders above and below your pay grade. And from interconnected business departments. They’ll have their own needs and pressures. Risks are ever-present in every decision and act or omission. You’ll have a team of your own and you’ll be part of a team. And there will be disagreements and, heaven forbid, politics involved.
So how can you lessen the pressure and remove obstacles to progress, and, ultimately, your success?
Arm Yourself with Knowledge
You may be a brand new, shiny maintenance manager or even an old, tired, or frustrated one. You may even be happy and fulfilled one. But it’s never too late to learn.
Let’s save you some time and look at the six facts you need to know.
1. Manage Upwards and Life Will Be Easier
Your manager – whether that be an engineering manager or plant manager, or both – will have expectations. These will most often be about performance and costs:
"Why is Line 4 down again? We’re nowhere near 70% OEE!"
"Why didn’t we have a spare cylinder on site? You said the stores were in good shape."
"How come overtime is so high? You’ve almost blown the budget 3 months early."
"Why does that engineer Brad never wear the right PPE? He’s got to go. It’s on you."
And that’s just the morning meeting.
Proactively manage their expectations and life will be easier. Pre-empt these types of questions and give honest answers, backed up with data.
Not everything is the fault of maintenance; use root cause analysis to understand where downtime really comes from, why procurement is not quite right, and why overtime has increased.
And… stand your ground when you know you’re right.
2. You’ll Be Pressured by Operations
If you’ve ever worked in maintenance, you’ll know this is almost always true.
In organizations with a good culture, it is a reasonable, honest pressure where problems are discussed openly and resolutions are reached amicably.
In bad cultures, it means being openly blamed for every production stoppage and having planned and agreed maintenance time cut short or eliminated altogether.
In the worst of cases, it can be an antagonistic relationship.
If you’re somewhere around the latter culture or even in between, then the first step is to have an open dialogue about teamwork, goals, and culture. The idea is that you sell the value of maintenance as a profit center that benefits everyone in the long term.
It is critical to have a healthy two-way, inter-connected relationship.
3. Service Providing is What It’s All About
Still thinking about the relationship with operations, maintenance is a service provider.
Think of the relationship you have with your local car garage when they replace your exhaust system or perform an annual service. They are providing a service to you as the asset operator of the car.
That said, the garage is not the asset owner and neither is your maintenance department.
Operations have full responsibility for asset ownership and, therefore, a duty to run the asset within its capability, clean it correctly, and release it for scheduled maintenance on time.
And so, it’s obvious: a healthy two-way, inter-connected relationship is vital.
4. Manage Risks or They’ll Manage You
Every waking moment we are all risk managers.
As a maintenance manager, you will be constantly making risk management decisions:
- Do I trust the content of the CBM report enough to replace the gearbox?
- Should we keep running the secondary boiler? Even though the inspector said the tubes are fouled.
- What will happen if we defer that PM inspection another week?
- Can I afford to pay the OEM to service the asset for two full days?
The key to managing this situation is to use a documented risk management framework and tools.
By documenting, assessing, and analyzing risks, you are at least managing them. ISO 31000 – Risk Management will help you here.
And it should be a maintenance team effort. Get other subject matter experts involved.
If you don’t proactively manage risks, they’ll manage to cause you no end of expensive issues.
5. Planning is Queen or King
Planning ties in neatly with risk management.
Planning = control = fewer headaches.
And if you’re a new maintenance manager, make sure you’ve got someone planning (and scheduling) maintenance work. Along with a CMMS/EAM, it is the heartbeat and living pulse of maintenance management.
You want and need maintenance work to flow in a controlled manner: new work requests and orders, spare parts, task lists, risk assessments, resources, time slots, feedback, follow-on work, and close out.
When done well, it is a beautiful thing.
And you’ll sleep better.
6. Delegate to Stay Afloat
One of the critical components of reducing maintenance management stress is to delegate.
You’ll likely have senior maintenance technicians, maintenance supervisors, or team leaders.
So, use them!
Many maintenance managers try to do everything: attend every meeting, make every spare part cost decision, get involved with breakdowns, have the most input on planning and scheduling, deal with contractors, write the permits, buy the doughnuts, and even make the coffee.
This cannot and will not work in the long run.
Delegate to others.
And what happens if you do?
You will be providing them with leadership opportunities, increased motivation, and job satisfaction. And it is a form of succession planning for your future replacement or stand-in.
Making Sense of it All
Maintenance managers will do well to focus on these six elements of their role in maintenance management.
Keep it simple:
- Manage upwards.
- Recognize the pressure.
- Provide a service.
- Manage the risks.
- Plan.
- Delegate.
If you can get ahead of the game and be proactive, you will find yourself with more time and resources to focus on the core, critical elements of your role.
What’s not to like?
A more controlled and lower-stress environment, no more coffee going cold, and probably better sleep.
But you might still have to wait for Zack from IT - there’s no silver bullet for that.